iTRAK Addresses Throughput and Maintenance Challenges
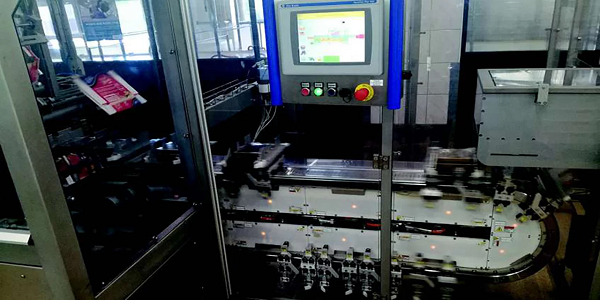
Original content by clicking this link
CASE STUDY | 5 minute read 🕛
Lotte Wedel, a leading Polish confectionary company, sees 50% throughput increase and less machine downtime thanks to intelligent track system.
〽️ Challenge |
|
🛠️ Solutions |
📉 Result |
|
Background
Founded in 1985 and based in Flonheim, Rheinland Pfalz, Germany, ECONO-PAK GmbH is as a leading manufacturer of packaging machines. Its long experience and the constant development of its product range means it can provide its customers with packaging machines and complete lines, including conceptual design, project planning and installation on site.
The company designs, develops and manufactures comprehensive and customised packaging machines and lines for the food and non-food sector, where it carries out the entire project management. It prides itself on simple machines with good accessibility that offer the best price/performance ratio, while delivering good efficiency and smooth handling of delicate products.
With exports to Europe, USA, Australia, South America, The Near East, Asia and Russia, food industry applications include the packaging of ice cream, pizza, fish, vegetables, fruit and meat; while primary non-food applications comprise dishwasher tablets, health products, automobile and electronic components.
In a recent project ECONO-PAK was approached by Lotte Wedel, a leading Polish confectionary company – and the oldest chocolate brand in Poland. The customer wanted ECONO-PAK to develop a packaging/cartoner machine that would more easily cater for varieties in packaging formats and product counts. The resulting machine developed by ECONO-PAK completely solved the intermittent speed, staggered transfer and chain wear issues faced by the customer in its existing machine, thanks to the deployment of an iTRAK® intelligent track system from Rockwell Automation.
Challenge
The problem with the traditional multi-servo-driven cartoner technology and Lotte Wedel’s specific project requirements was that when product counts – in this instance chocolate pralines in tray-type blister packages – were doubled or trebled prior to cartoning, its existing machine had to work intermittently to cater for additional product drops. Due to its common-chain drive and the fact that it was tuned to cater for single trays, the existing machine’s speed was governed by the slowest step in the packaging procedure. Packing a constant production flow of trays in single, double or triple packs requires a system capable of running high-speed continuous motion, combined with up to 90 intermittent steps per minute.
In addition to greater packaging flexibility in terms of counts, package sizes and shapes, Lotte Wedel was also looking for an increase in throughput – to keep pace with growing customer demand. ECONO-PAK was therefore challenged with increasing the line speed by at least 50%, from 120 to 180 products per minute, with an actual target speed of 170. Elevated packaging quality levels were also a major part of the brief.
Solution
ECONO-PAK was able to solve all of the issues faced by Lotte Wedel with a new machine concept based around the innovative iTRAK intelligent track system from Rockwell Automation.
iTRAK is revolutionising the design and build of track-based solutions for packaging and materials handling. By combining linear and rotary motion, it delivers a flexible, fully integrated solution that helps machine designers achieve a new paradigm in packaging and handling efficiency and throughput.
According to Rainer Bersch, Area Manager – Design & Order Processing: “We have been working with Rockwell Automation for decades and the customer also had an installed base of Allen‑Bradley® products, so Rockwell Automation was high on the list of potential automation suppliers for this new solution. What we were looking for was a system that could collect the products independently and then deliver them to the cartons. Importantly, the longer dwell times to pick up more than one product should not affect the overall speed of the rest of the system. It was for this reason that iTRAK became an obvious contender."
“We started with a kick-off meeting with engineers at Rockwell Automation,” he continues, “and we visited a sample iTRAK system at the Rockwell Automation OEM Competency Centre in Bologna in Italy. This marked the beginning of a common development programme between the two companies as we both worked towards an iTRAK-based solution that would address the needs of Lotte Wedel. iTRAK is also closely tied into the Rockwell Automation Integrated Architecture concept, so we knew we could develop a completely integrated automation infrastructure.”
In operation, the iTRAK solution with movers and linear drive sections positions an independent shuttle (attached to a pair of movers) under the product infeed, where it collects between one and three blister packs/trays. It then moves rapidly and smoothly to the packaging station where the products are side loaded into open cartons that run on another line parallel to the iTRAK circuit. By using independently controlled shuttles, the longer dwell time at the product in-feed station (when more than one tray is deposited) has no effect on the overall speed of the machine, which would be the case with a system driven by a common chain or conveyor. Once empty, the shuttles then traverse rapidly back around the track to sit momentarily in a ‘holding area’ prior to being moved back into position to be loaded with the next batch.
Primary control is delivered by an Allen‑Bradley CompactLogix programmable automation controller, with additional motion axes being manipulated by Allen‑Bradley Kinetix 5500 servo drives. Allen‑Bradley PowerFlex® variable-speed drives control some of the other machine movements and an Allen‑Bradley PanelView™ Plus 1000 HMI delivers operator interactions. The entire solution – a graphic demonstration of the Rockwell Automation Integrated Architecture – is programmed on one single development environment – Studio 5000.
“The infeed and the carton pusher are now completely separated,” Bersch explains. “This simply wasn’t possible in the past with the older common-chain machine. Lotte Wedel can now use a wider variety of product counts on the same machine, without having to worry about extended infeed processes slowing the machine down.”
Results
ECONO-PAK and Lotte Wedel benefited from significant programme support, delivered by Rockwell Automation Global OEM Technical Consultants (GOTC) and engineers from Germany and the USA. As part of the development collaboration, this included design and programming support for calculations regarding shuttle counts, motion profiles and target speeds.
The unit was then tested in the USA and delivered, complete with the guidance system, before being assembled and pre-tested prior to start up. “During the installation,” Bersch continues, “we undertook commissioning with a Rockwell Automation programmer on site; and for the site-acceptance testing there was only one eight hours trial run necessary, which delivered 100% efficiency.
“Lotte Wedel now has a machine which is infinitely more flexible in terms of packaging counts and can be easily adapted to cater for other product formats and shapes,” Bersch expands. The customer is also seeing less downtime, increased performance and improved asset utilisation.
ECONO-PAK was able to deliver this machine through a combination of its existing expertise and the technical help from Rockwell Automation. “We definitely learnt something from each other during the collaborative development process,” Bersch concludes. “We learnt about how we can develop innovative machines using iTRAK and the Rockwell Automation engineers now have another example of iTRAK in action, based on our experiences of machine design and the packaging industry. The programming and after-sales support has been highly effective and we are already discussing additional similar projects for the US market.”
Allen‑Bradley, CompactLogix, iTRAK, Kinetix, LISTEN. THINK. SOLVE., PowerFlex, PanelView Plus, Rockwell Automation, Studio 5000 are trademarks of Rockwell Automation, Inc.
Trademarks not belonging to Rockwell Automation are property of their respective companies.
Original content by clicking this link