iTRAK Helps OEM Slash Changeover Times By Up To 50%
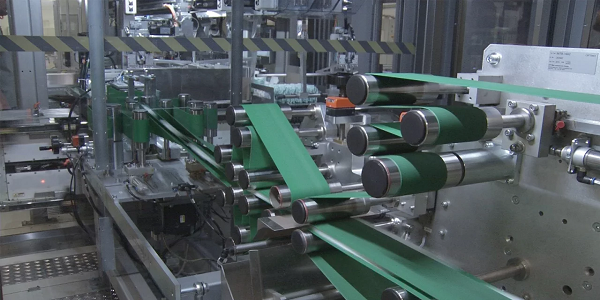
Original content by clicking this link
CASE STUDY | 6 minute read 🕛
Optima and Intigena realize the benefit of iTRAK coupled to modern, flexible Integrated Architecture solution from Rockwell Automation. Changeover times cut by as much as 50%.
〽️ Challenge |
|
🛠️ Solutions |
📉 Results |
|
Background
Optima Nonwovens, a member of the OPTIMA Packaging Group GmbH, develops leading-edge technologies for packaging paper hygiene products.
The company’s systems cover the complete range of automated packaging processes, from the intake of products right through to being palletized for shipment.
Products include nappies, sanitary towels, bathroom tissue rolls and wet wipes.
The company’s solutions offer impressive format flexibility, and are able to process everything from small packages to jumbo packs on a single machine, in accordance with the increasingly diverse product variations and requirements of the international markets.
Inspection functions and secondary packaging capabilities are integrated to achieve complete automated lines.
Optima Nonwovens actively seeks out and employs state-of-the-art engineering technologies in its development and project planning and that led it to develop a new diaper (nappy) bagger/stacker for its customer Intigena Produktion, one of Europe's leading suppliers of hygiene products.
The new machine employs the revolutionary iTRAK® Intelligent Track System from Rockwell Automation.
Not only has this technological deployment resulted in far greater flexibility for rapid product-format changeovers, it has also helped to increase the overall equipment effectiveness (OEE) of the machine.
OPTIMA Packaging Group GmbH is a member of the Rockwell Automation PartnerNetwork™ program as an OEM Program Participant at partner level.
Members of the Rockwell Automation OEM Program demonstrate a commitment to offer high-quality, innovative machines and equipment that help manufacturers improve business agility, optimise productivity, and increase business performance.
Through the use of Rockwell Automation products, technology and industry expertise, these PartnerNetwork members also help end users achieve sustainability and safety-compliance objectives.
Challenge
The previous-generation machine used a long belt, with fixed-pitch paddles for transportation and grouping of the product to be packaged.
This configuration meant that any product changeovers – especially those relating to the size of the product – required significant re-engineering to adjust the belts to match the new product sizes.
In isolation, these changeovers were not too long, but when four or five were required on a shift, the cumulative downtime soon added up.
Solution
With 95% of its machines already benefiting from the deployment of Allen‑Bradley® products from Rockwell Automation, the move over to an iTRAK solution was a natural progression for Optima.
The iTRAK solution comprises multiple movers running on straight and curved paths, all of which can be independently controlled; instantly removing the limitations of fixed-pitch belt systems.
Its highly innovative capabilities combine both linear and rotary motion, resulting in a flexible, fully integrated solution that can increase production throughput, reduce maintenance and overall machine size and, in this instance, slash machine changeover times.
The iTRAK system is part of a Rockwell Automation® Integrated Architecture® solution, which is used to both actuate and control the majority of the machine’s primary functions.
At the heart of the automation infrastructure is an Allen‑Bradley ControlLogix® programmable automation controller (PAC) working in conjunction with an Allen‑Bradley PanelView™ Plus 7 operator interface.
In addition to the iTRAK servo solution, the machine deploys a number of more-traditional servo motors and Allen‑Bradley Kinetix® 6000 multi-axis servo drives.
These servo solutions are used for a number of steps and functions, including pushing the diapers/nappies into the packs, driving the belts to move the products between stations, the turntables, the two product compression steps, product positioning, bag welding, bag extraction and final movement to the take-out conveyor.
An EtherNet/IP network reduces overall wiring on the machine and also offers easier integration with factory and office communication systems and access to the Connected Enterprise.
In operation, individual nonwoven products are taken from the manufacturing machine by the stacker and then counted and grouped into standard sequences.
The high-speed stacker provides the first compression step, before a pusher transfers the separate product stacks to the handling unit that is connected to the bagger.
The stacks are compressed again and are turned around and positioned either as layers or rows and transported onto the bagger.
In the bagger, foil bags are fed in and the product stacks are forwarded to the main compression process.
A pusher loads these product stacks into the iTRAK system where they are then moved and positioned individually using the iTRAK movers and pushed into the bags.
The bags are then sealed and forwarded for further processing, such as secondary packaging.
Results
Oliver Rebstock, Managing Director at Optima explains: “This machine represents the cutting edge of current technological possibilities in the packaging of nonwovens products.
Intigena could now process up to 1,600 products per minute with this new high speed stacker design and we have eliminated the previous bottleneck in the stacker infeed.
“In operation, Intigena benefits from clearly reduced format changeover times, with a reduction of some 15 minutes or 50% per format changeover,” Rebstock continues.
“The transport cassettes are adjusted accordingly for a change to a thicker or thinner diaper or for a different product count.
The transport cassettes are adjusted solely from the HMI and can be done so during production. What is more, during this time, the tightening function for stabilising the products in the cassettes is maintained.
“The simplified format change has a noticeable positive influence on Overall Equipment Efficiency (OEE),” Rebstock elaborates, “even when there is only one format change per shift.
Many nonwovens companies however report ever more frequent format changes – even four changes per shift are no longer rare. In this instance it is clear to see where rapid changeovers offer a huge time saving advantage.”
According to Helmut Krasko, account manager at Rockwell Automation, the iTRAK solution removes all the limitations of a belt-driven infrastructure.
“And if you want to extend the line you simply add more movers. Previously, changes to the product size or packaging format meant multiple mechanical adjustments were required.
Using iTRAK, this is all done automatically by the PAC via input from the HMI.”
Significant research and tuning of the iTRAK system was undertaken, with the help of engineers and a Rockwell Automation GOTC (Global OEM Technical Consultant), in order to optimise the iTRAK operation to suit the specific demands of the application; including the acceleration and deceleration profiles and the compression steps.
Rockwell Automation GOTCs are responsible for product and technology adoption with partner OEMs and have extensive domain knowledge of the industry and applications being served along with in-depth knowledge of the Rockwell Automation products, technology and system architecture in order to provide domain level expertise consulting.
“The previous packaging system from Optima was in use for many years and was very much acclaimed in the company,” explains Claus Ullrich, Technical Director at Intigena Produktion.
“All of our expectations regarding this new machine were fulfilled. The machine was here in good time and was ready-to-operate after only a few days.
And with the experience of the first installation, the time taken to commissioning the second line was reduced to just one week.
“We are facing market challenges where our customers require different kinds of packaging, stacking, and contents,” Ullrich continues, “so we have to react quickly and deploy manufacturing solutions that deliver faster changeovers.
We had to find new solutions; and as well as flexibility we needed to increase machine throughput. The former solution from Optima was limited by speed – it simply couldn’t go any faster using chains – so this new iTRAK-based machine is making a huge difference.
We are now capable of running the packaging process at higher speeds while still achieving the packaging quality our customers demand.
The machines have been running for one year now and the results are very promising.
We achieved the stated performance demands within a very short time and there are still possibilities to go even faster and run the lines at even higher volumes.
“We are particularly interested in The Connected Enterprise® concept, in relation to the IoT and Industrie 4.0.
A more connected infrastructure means that two-way communication between us and other people in the value chain will result in even greater efficiencies.
The collection of real-time manufacturing data, which can be actioned immediately, is also of huge benefit and will help us to improve our packaging operation even further.”
Original content by clicking this link