Un único proveedor multidisciplinar ofrece numerosas ventajas
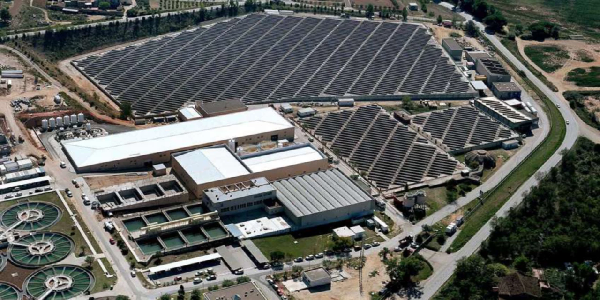
Contenido original: rockwellautomation.com/es
CASO PRÁCTICO | 9 minutos de lectura 🕛
Gracias a un programa de mejoras y ampliaciones de planta, una importante distribuidora de agua española disfruta de las múltiples ventajas de la adopción de las tecnologías y de los servicios más punteros de Rockwell Automation.
🔎El desafío |
ATLL debe proporcionar agua potable independientemente de la calidad del suministro local del río, que cambia constantemente cada día. |
🛠️ Las soluciones |
|
📈 Los resultados |
|
Antecedentes
Aigües Ter Llobregat (ATLL), empresa concesionaria de la Generalitat de Catalunya SA, cuenta con las certificaciones ISO9001-2000, EMAS, ISO 14001-2004, UNE 1600:2010 y OHSAS 18001 suministra agua potable a más de cien municipios a través de su red regional desde los ríos Ter y Llobregat así como de agua de mar desalinizada.
La aportación de Rockwell Automation se puede apreciar mejor si la dividimos en tres áreas: gestión de activos de una extensa infraestructura de automatización y control geográficamente dispersa, instalación del sistema Arquitectura Integrada para el control de la planta de electrodiálisis reversible más grande del mundo, y un sistema de monitorización en línea de condiciones que contribuye a la implementación de una exhaustiva estrategia de mantenimiento predictivo.
Las soluciones
FactoryTalk® AssetCentre
ATLL tiene que suministrar agua potable independientemente de la calidad del agua de los ríos locales, que cambia constantemente todos los días. A diario, durante los distintos turnos de trabajo, los ingenieros de control de ATLL deben hacer frente a múltiples cambios en los puntos de ajuste de los PLC para responder a las diferencias en la calidad del caudal de agua entrante. ATLL utiliza aproximadamente 230 PLC (PLC5, SLC500 y ControlLogix) en combinación con 210 paneles de operador PanelView. Cuatro empleados se encargan de la ingeniería y del mantenimiento de los PLC. Entre ellos se incluye un integrador de sistemas. A pesar de que los PLC se encuentran distribuidos a lo largo de más de 2000 km2, todos se pueden monitorizar desde una estación central gracias a la comunicación por satélite.
ATLL ha invertido tiempo, dinero y esfuerzo para obtener las certificaciones IS09001-2000, ISO14001-2004 y EMAS con el fin de demostrar a sus clientes que puede suministrarles agua de forma ininterrumpida, con un grado de calidad constante y respetando los requisitos medioambientales en todo momento. Teniendo en cuenta todos estos factores, la monitorización de los activos es de vital importancia, sobre todo en lo que respecta a los cambios realizados en los PLC. Por lo tanto, para ATLL es muy importante supervisar el acceso a los equipos de control sin perjuicio de la gestión de su mantenimiento.
ATLL colaboró directamente con Rockwell Automation en la instalación de la solución de gestión del FactoryTalk® AssetCentre y la modificación de su infraestructura de IT. En la actualidad, la solución administra aproximadamente 100 PLC, además de dos PC de sobremesa que utilizan los empleados de ATLL y el integrador de sistemas. Las funciones implementadas comprenden: control de acceso, un sistema de auditoría, un plan de respaldo y de recuperación ante desastres, y una solución de informes. Entre sus ventajas se incluyen la posibilidad de monitorizar los cambios de parámetros específicos que afecten la calidad del agua y la exactitud de los caudalímetros, el intercambio más eficaz de la información y el conocimiento entre los ingenieros de control que trabajan en distintos turnos, la prevención de los problemas de los PLC cuando varios contratistas trabajan simultáneamente en las instalaciones, y la seguridad que ofrece la puntual realización de copias de seguridad.
ATLL quiere mejorar sus operaciones de mantenimiento a través de la implementación de un completo plan de recuperación ante desastres que permita a los PLC, junto con la interfaz operador-máquina, suministrar agua de calidad de forma ininterrumpida incluso en caso de que se produzca una emergencia. La solución FactoryTalk AssetCentre permitirá a ATLL demostrar que cumple específicamente los reglamentos relativos al control de los activos industriales, como parte de los requisitos de ISO9001-2000.
Arquitectura Integrada™ de Rockwell Automation
Gracias a la ampliación de las instalaciones, la estación de tratamiento del agua potable (ETAP) de Llobregat ha incrementado su producción de 200.000 a 345.000 m3/día.
El proyecto, cofinanciado por el Fondo de Cohesión de la Unión Europea, tiene como objetivo mejorar la línea de tratamiento, ya que el agua procedente de la zona baja del río Llobregat presenta problemas de salinidad y contaminación (trihalometanos) que dificultan el proceso de purificación. Por este motivo, ATLL necesitaba poner en marcha una planta de desalinización basada en un sistema de electrodiálisis reversible (EDR) que mejorase las propiedades químicas y organolépticas (sabor y olor) del agua.
Otro de los retos era aumentar el nivel de automatización de la planta. Todos los componentes de control y de las instalaciones deben monitorizarse desde una estación central. De este modo, las 100.000 señales existentes se incrementarán con 30.000 señales nuevas (distribuidas a lo largo de una extensión de 2000 km2) que serán monitorizadas en tiempo real desde la sala de control, donde se regulará el funcionamiento de la red de distribución regional. Por último, la elevada disponibilidad de la instalación también es una cuestión legal: un paro de la producción de agua potable es inadmisible, aunque solo se prolongue unas cuantas horas. Este factor implica una estructura paralela del proceso de la planta y la necesidad de una solución de control fiable, flexible y escalable.
En colaboración con ATLL, Rockwell Automation y EBE Asociados desarrollaron una avanzada solución de automatización para la nueva planta basada en el sistema Arquitectura Integrada de Rockwell Automation. Esta solución de control integra 11 PLC ControlLogix®, de los cuales, nueve se encuentran en el sistema de electrodiálisis reversible, subdivididos en nueve líneas de producción completamente independientes. De este modo, los ingenieros solo tienen que detener una novena parte de la planta si se produce algún incidente. Cada uno de estos PLC se conecta a un panel de operador PanelView™ Plus 1250 que permite monitorizar y manejar cada una estas nueve líneas a escala local. Las E/S se dividen en cuatro estructuras ControlLogix a distancia, y las E/S descentralizadas en las instalaciones se configuran mediante tres estructuras de tarjeta FLEX™ I/O.
Todos los controladores, los paneles de operador y las entradas y salidas descentralizadas se conectan mediante una red ControlNet™ redundante, que garantiza un alto grado de disponibilidad de datos en cualquier situación. Cada una de las nueve líneas de producción cuenta con redes DeviceNet que permiten accionar las válvulas. En resumen, la planta desalinizadora incluye un total de nueve redes ControlNet redundantes, 18 redes DeviceNet™ y un total de 10.200 señales, de las cuales 1000 son analógicas para su procesamiento.
Los otros dos controladores ControlLogix redundantes gestionan la estación de bombeo, los lechos de cal, el control de adición de sustancias químicas y los componentes auxiliares de la instalación. Las entradas y salidas se distribuyen en las instalaciones mediante tarjetas FLEX I/O y se conectan a través de una red ControlNet redundante. Todos los controladores se agrupan en la sala de control central a través de una red EtherNet/IP™ con topología en anillo de fibra óptica, que configura los medios ideales para la visualización de todos los parámetros procedentes de cualquier dispositivo en tiempo real.
La gran versatilidad del sistema Arquitectura Integrada, que aúna plataformas de controladores multidisciplinares Logix, arquitectura de redes abiertas NetLinx, plataforma de visualización View y servicios de información y datos FactoryTalk, ofrece el más alto nivel de fiabilidad, flexibilidad y capacidad de escalado que requiere la consecución de los objetivos establecidos al inicio del proyecto.
Los resultados
Monitorización de condiciones en línea
ATLL tiene experiencia en el uso de sistemas de mantenimiento predictivos basados en las lecturas de vibraciones de las máquinas a través de colectores de datos portátiles. En este caso, la ventaja radica en la posibilidad de medir un gran número de máquinas en una planta con una inversión reducida en adquisición de instrumentación y software. Por otro lado, también se plantea el problema del coste que conlleva todo un equipo humano con formación en estas técnicas y la falta de información en tiempo real sobre el estado mecánico de los equipos que se consideran esenciales para el proceso.
Unas de las instalaciones más importantes de la planta es el punto de admisión de agua. Éste contaba originalmente con cuatro bombas verticales que han sido ampliadas a ocho. Tras un exhaustivo análisis de las opciones disponibles en el mercado para la monitorización en línea de la vibración, la temperatura y los parámetros críticos, ATLL eligió una solución de Rockwell Automation basada en la familia XM. A continuación se detallan los motivos de esta decisión.
Máquinas de velocidad variable
En las instalaciones donde se utilizan variadores para regular la velocidad de motores se ha logrado una reducción del consumo energético de hasta el 50 %. En ellas, las cargas centrífugas, como el agua, son reguladas mediante bombas que funcionan a entre el 100 y el 80 % de su capacidad. En consecuencia, las máquinas empleadas deben contar con un control de velocidad muy preciso para regular el caudal y, desde el punto de vista mecánico, con algunas medidas de seguridad para su funcionamiento y mantenimiento. La entrada de tacómetro presente en los dispositivos de control de vibraciones de la serie Allen‑Bradley XM120 permite relacionar directamente el nivel de vibración con la velocidad de funcionamiento. De este modo, el valor de vibración puede ser controlado como múltiplo de la velocidad de giro (1x, 2x, 3x, etc.) de forma permanente. Esta información, junto con la lectura de fases, es de vital importancia cuando se arrancan y detienen las bombas y en condiciones de uso normales, ya que permite determinar las frecuencias críticas y de resonancia del conjunto del sistema.
Sistema distribuido
El precio del cobre, el coste de mantenimiento del cableado y los avances en las comunicaciones han favorecido el uso de fieldbus y han dado lugar a un nuevo concepto de arquitectura distribuida. En ATLL se han conectado cuatro canales de vibración, un tacómetro y seis canales de lectura de temperatura a las unidades XM correspondientes, instaladas en un armario pequeño junto a cada una de las bombas. Cada uno de estos armarios se comunica a través de DeviceNet en tiempo real. A su vez, éstos están conectados a otros dispositivos distribuidos como: un controlador ControlLogix, un convertidor XM500 y un par de paneles de operador PanelView 1250 para las tareas de monitorización y control. El controlador también establece un puente entre la red de campo DeviceNet y la red Ethernet de la planta.
Limitaciones de los transmisores de 4-20 mA
La primera de las limitaciones encontradas fue que estos transmisores están diseñados para funcionar con rangos de amplitud y frecuencia predeterminados. Esto restringe el uso de un transmisor específico en relación con una amplitud aproximada para cada tipo de máquina. Además cabe la posibilidad de que los rangos de frecuencias medias, siempre fijos, no filtren los niveles de vibración procedentes de otras máquinas, e incluso de que no puedan detectar problemas mecánicos, como fallos de los cojinetes, por la incompatibilidad de rangos o de unidades de medida. El uso de estas sondas obligaba a cablear cada canal de punto a punto, y a disponer de tarjetas en el punto de recepción (controlador) compatibles con las señales analógicas, con el consiguiente coste adicional.
ATLL eligió la solución XM porque permite instalar sondas de vibración estándar (acelerómetros) sin limitaciones de rangos de frecuencia o amplitud, y sin distinción entre ellas, ya que la configuración del punto y la máquina se llevan a cabo durante la programación de las unidades XM, y no al seleccionar la sonda.
Capacidad de análisis
ATLL valora especialmente el hecho de que los dispositivos sobre el terreno dispongan de la información necesaria para realizar un diagnóstico avanzado. Cada unidad de vibración XM 120 tiene capacidad para medir más de 30 parámetros de vibración en tiempo real: espectro FFT, forma de onda, cuatro bandas configurables para frecuencia y velocidad de giro, niveles de amplitud independientes con respecto al tipo de fallo (desequilibrios, desalineamientos, cojinetes, etc.), estados de sensor, registro de archivos e inhibición de alarmas en relación con la velocidad de la máquina. Esta información se procesa a escala local en cada unidad para después ser transmitida al controlador ControlLogix y a los distintos sistemas y departamentos de la planta. De este modo es posible conocer en tiempo real el estado general y los parámetros de las bombas. El personal responsable del mantenimiento debe también disponer además de información más detallada, como el análisis de onda de espectros, que debe quedar registrada en la base de datos del programa Emonitor.
Conclusión
La instalación del sistema más moderno de predicción con fines de protección y monitorización en línea ha permitido a ATLL integrar toda la información sobre el estado de las bombas de suministro de agua en el sistema de control de la planta. Estos datos serán de gran utilidad para las operaciones generales y para adaptar los planes de mantenimiento a las condiciones reales de las máquinas de forma más eficaz. Además, el sistema se puede ampliar fácilmente al resto de los equipos críticos de la planta.
Los resultados antes mencionados son específicos para el uso de productos y servicios de Rockwell Automation por parte de este cliente junto con otros productos. Los resultados específicos pueden variar para otros clientes.