Toma de decisiones autónoma para manejo de materiales
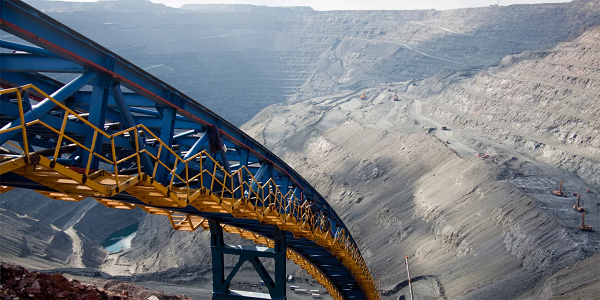
Contenido original: rockwellautomation.com/es
CASO PRÁCTICO | MINERÍA | 4 minutos de lectura 🕛
Una importante empresa minera reduce los retos en torno al manejo de materiales para mejorar las operaciones.
〽️Desafío |
El manejo de materiales involucra desafíos intrínsecos que toda empresa minera debe afrontar para enviar el producto adecuado en el momento adecuado. La reubicación no programada de los equipos, la falta de estandarización de los procesos y la variabilidad de los operadores pueden derivar en costos adicionales a través de la cadena de suministro. Un importante cliente minero quiso asegurarse de que el material se enviaba según el calendario previsto a fin de reducir sus costos operacionales. |
🛠️Soluciones |
Rockwell Automation ha desarrollado una completa solución de automatización de decisiones para el manejo de materiales basada en FactoryTalk ProductionCentre y controladores Logix. Esta solución le ayuda a cumplir sus metas de productividad, calidad, cumplimiento del calendario y reducción de costos. La solución utiliza un gestor de ejecución en tiempo real para mejorar las eficiencias operacionales a fin de lograr el cumplimiento normativo. |
📉Resultados |
|
Los equipos de manejo de materiales son un elemento fundamental de la cadena de suministro en minería. Son esenciales para el desplazamiento, almacenamiento, mezclado y entrega de materiales en toda la mina, además de servir de conexión entre la mina y el mercado. Aunque en principio parece sencillo, cuando se trata del manejo de materiales en minería, una empresa minera debe enfrentarse a numerosos desafíos.
El manejo de materiales en minería es inherentemente difícil. Hay que trabajar con máquinas gigantescas que transportan enormes cantidades de materiales a lo largo de grandes distancias, por lo que un problema en las fases iniciales se propagará en cascada por toda la mina y por la cadena de suministro. Antes de que pueda darse cuenta, tendrá que lidiar con demoras, tiempo improductivo, despilfarro y retrasos importantes. Ninguna empresa minera es inmune a estos desafíos, pero para muchas, acabar con la variabilidad es un factor clave.
El problema de la transferencia
La transferencia de materiales ha sido desde siempre un proceso complejo. Si no se dispone de un sistema completamente automatizado, los operadores se verán abrumados por la necesidad de tener que realizar varias tareas y gestionar varias interfaces. Dado que estas entregas constantes se producen en todas las fases de la cadena, muchas empresas son susceptibles a retrasos no programados del proceso, despilfarro y la falta de estandarización a causa de la variabilidad de los operadores y a los problemas de comunicación.
Un día en el sistema de carga de trenes (TLO)
El controlador de carga es el punto central de las operaciones de planta, lo que implica que durante los momentos más agitados del día, tendrán que encarar múltiples desafíos de manera simultánea. El operador de TLO puede verse rápidamente abrumado por todas las fuentes de información que necesita consultar. Aquí es donde los errores comienzan a acumularse.
Una de las consecuencias más comunes de verse abrumado es que los equipos no estarán en el lugar adecuado en el momento adecuado para cargar un tren, lo que producirá retrasos en el tren y un impacto negativo que se irá amplificando a través de la cadena de suministro. Trabajar de esta manera tan reactiva no ofrece ninguna oportunidad de emplear indicadores predictivos que señalen dónde puede haber un problema antes de que este aparezca.
Un paso en la dirección adecuada
Una importante empresa minera se propuso superar los desafíos que enfrentaba en la operación de TLO. ¿La solución? Automatización de decisiones (gestión de ejecución) de manejo de materiales mediante FactoryTalk ProductionCentre y controladores Logix.
Una vez implementada, la solución coordina los recursos de la mina del cliente y la gestión de ejecución (EM) automatiza la organización del proceso de toma de decisiones en torno a los equipos. La EM se encarga de ello mediante su integración con el SAP y/o con el sistema de gestión de trabajos del sitio, para convertir automáticamente un trabajo en una lista de todas las tareas y equipos necesarios para ejecutar correctamente el trabajo.
La EM se integra con los sistemas de control existentes a fin de alinear los diferentes equipos necesarios para llevar a cabo el trabajo. Una vez habilitados los permisos del sistema de control existente para la ruta y los equipos, el trabajo de apilamiento/recuperación comenzará automáticamente. La EM actualizará continuamente el sistema de gestión del inventario de apilado así como el sistema SAP en torno a los avances del trabajo. Una vez finalizado el trabajo, la EM reubicará automáticamente los equipos en los lugares adecuados para el siguiente trabajo.
La solución está compuesta de dos componentes principales. En primer lugar, el gestor de producción define el número de trabajo, la cantidad de trabajo y el tipo de material. En segundo lugar está la gestión de la ejecución en tiempo real (REM). La REM dirige el gestor de producción, coordinando el inicio o la finalización de un trabajo, midiendo los consumos de materiales y la producción de materiales. La función de la REM es dirigir y organizar el sistema de automatización de cada área, para asegurarse de que todas las operaciones completarán correctamente el trabajo.
Maximización del ROI de los activos
La implementación fue sencilla. La gestión de la ejecución (EM) se integra con el sistema de control existente, por lo que todos los sistemas de control y de seguridad se mantienen intactos. Una vez concluida la implementación, los beneficios superaron las expectativas de la empresa. Se observó de inmediato una mejora en la programación de la conformidad gracias a una estandarización de los procesos operativos más eficientes de las instalaciones. El cliente también logró una reducción de la carga de trabajo y de la dependencia en torno a los operadores, además de disminuir los retrasos no programados del proceso. Esta solución produjo un ahorro anual de 200 millones de dólares para la empresa.
Contenido tomado de: rockwellautomation.com/es