Smelting Plant Optimization
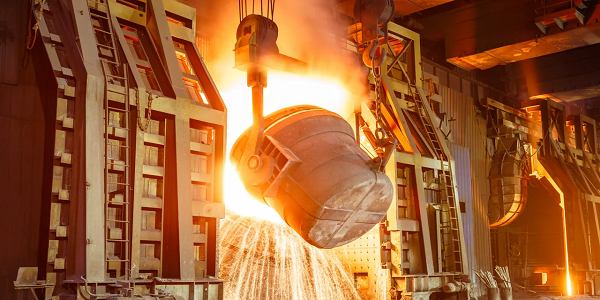
Original content by clicking this link
CASE STUDY | 1 minuto de lectura 🕛
Arena Simulation helps to improve understanding of your overall systems to make smart decisions going forward.
〽️ Challenge |
Understanding and resolving a number of plant bottlenecks. |
🛠️ Solution |
Combining thermodynamic modelling (Factsage®), heat and mass balance modelling (Metsim®) and now dynamic simulation (Arena), the Extractive Metallurgy Group at XPS can be considered a leader in metallurgical modelling. Arena® simulation software is well adapted to the modelling of a complete metallurgical plant having a number of complex and interacting operations. All types of unit operations can be incorporated into the model. This can range, for example, from systems for materials handling - feed conveyors, slurry pumping or crane and ladle transfers - to individual unit operations such as a high temperature smelting furnace, a leach tank or a milling operation. |
📉 Results |
|
Background
Dynamic simulation is the time-based simulation of an operating plant or process such as a copper smelter. Computer-based dynamic simulation has become an increasingly power tool over the last two decades aimed at optimization of complex industrial operations. The ability to dynamically simulate a given plant or process over time, such as a week or a year of operation including running times and potential downtimes, can provide invaluable insight to the understanding of a plant. This can help in projects to increase throughput, plant de-bottlenecking exercises, or in brownfield expansion projects (discrete event modelling).
Without having a high level look at how your systems are all working together, it's difficult to make decisions. Understanding your bottlenecks, capacity constraints, and other issues, will allow you to make informed decisions to improve your day to day operations. This plant was facing exactly this issue and needed a tool to understand their opportunities.
Solution
By implementing Arena Simulation Software to develop a model, the team was able to understand the system from raw materials entering to final products leaving. The clarity into their systems allowed them to identify bottlenecks and other key areas of improvement. Using this data, they were able to implement changes quickly and efficiently.
Results
- Understanding and resolving a number of plant bottlenecks to allow full plant entitlement to be reached
- Determining plant capacity under certain upset conditions (such as maintenance situations, unexpected shutdowns, etc.).
- Optimizing operating schedules
- Overall flow-sheet optimization
Original content by clicking this link