Doosan Bobcat: Una planta digital propulsada por personas
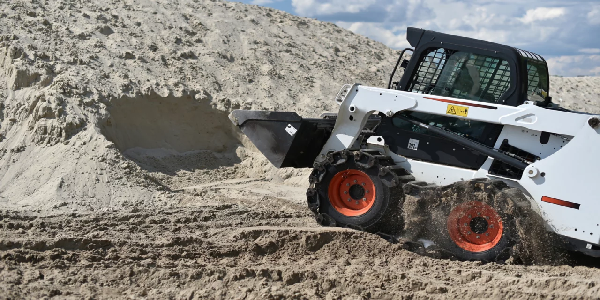
Contenido original: rockwellautomation.com/es
CASO PRÁCTICO | LIDERAZGO INTELECTUAL EN LA TRANSFORMACIÓN DIGITAL
4 minutos de lectura 🕛
El compromiso temprano de los empleados ayudó a la empresa a aportar más inteligencia basada en datos a la planta de fabricación en la República Checa.
No hay muchas empresas que puedan decir que crearon toda una industria, pero eso es exactamente lo que hizo Bobcat Doosan al inventar la cargadora frontal compacta y dar lugar a la industria de equipos compactos.
Tras más de 60 años, la empresa ha continuado innovando no solo su gama de equipos, sino también las operaciones de fabricación que producen dichos equipos. Un buen ejemplo es el trayecto hacia la transformación digital que la empresa acaba de emprender en su planta de fabricación en Dobris, República Checa.
La planta forma parte de la sede central europea de la empresa, produce más de 12,000 máquinas al año y cuenta con más de 600 empleados. Mediante la iniciativa, la empresa deseaba aumentar la capacidad de producción y la garantía de calidad en la planta, así como eliminar o minimizar las tareas sin valor agregado.
Aunque la tecnología desempeñaría un papel clave en el proyecto, la empresa también sabía que otro elemento era esencial: sus empleados.
Construcción de una mejor inteligencia
Antes de la iniciativa digital, existía una falta de visibilidad de los datos en la planta en Dobris. Se habían integrado muy pocos silos de datos. Los datos operativos se recolectaban manualmente y se introducían en archivos Excel. La falta de tableros dificultaba que los empleados de la planta tomaran acciones impulsadas por datos.
Esto dio lugar a desafíos como, por ejemplo, baja eficacia total del equipo en la zona de fabricación, lo cual afectó la capacidad de producción.
"Cuando empezamos esto, todo estaba basado en papel y los datos se almacenaban en silos", dice Hiram Sosa, gerente sénior de automatización de Doosan Bobcat. "Por eso había muchos datos disponibles. Una de nuestras misiones era enfocarnos en lo que denominamos TDK: transferencia de datos en conocimientos”.
Para mejorar las operaciones, Sosa y su equipo deseaban conectar el equipo y los dispositivos de la planta para eliminar los silos de datos. También querían implementar una plataforma de Internet industrial de las cosas para recolectar y visualizar datos. Esto ayudaría a los empleados de la planta a tomar mejores decisiones y a reducir el tiempo sin valor agregado que se dedica a recolectar y administrar datos.
Una implementación de IIoT propulsada por las personas
Un equipo de liderazgo principal, constituido por representantes con funciones tales como la producción, la calidad, la automatización digital y las cadenas de suministro, se encargó de la implementación. Se estableció un nuevo consejo digital para supervisar este y todos los demás proyectos digitales, y proporcionar gobernabilidad y estandarización.
Como plataforma de Internet industrial de las cosas, el equipo eligió FactoryTalk ® InnovationSuite, propulsada por PTC. La solución se conecta a diferentes tecnologías de la planta y recolecta, contextualiza y organiza los datos.
La implementación no se trató solamente de instalar la tecnología y transferirla a los empleados de la planta. Por el contrario, el equipo deseaba involucrar a los empleados como una parte clave del proceso.
"Una de las cosas que hicimos al principio fue organizar lo que llamamos el "día de la tecnología", comentó Sosa.
Como parte de este evento, los empleados en todos los niveles pudieron ver los tableros y el sistema de generación de informes autónomo, y probar nuevas tecnologías tales como la realidad aumentada. No solo pudieron familiarizarse con las nuevas tecnologías, sino que pudieron hacer preguntas y ofrecer nuevas ideas para allanar el camino para las implementaciones de tecnología en el futuro.
Cuando llegó el momento de implementar la plataforma, el equipo identificó oportunidades para optimizar la capacidad de producción y la calidad.
"Una de las cosas en las que nos enfocamos es ofrecerles la mejor calidad a nuestros clientes y también a nosotros mismos", explicó Sosa. "Por eso, implementamos algunas de las capturas de datos para el equipo a fin de mejorar la garantía de calidad".
Resultados iniciales
La planta en Dobris ya ha experimentado las ventajas de la iniciativa de transformación digital. Más tomas de decisiones impulsadas por datos, así como una reducción de la recolección y el procesamiento manuales de datos, han ayudado a aumentar la productividad y la garantía de calidad. Y la zona de fabricación ha podido aumentar la OEE entre un 10 y un 15%.
"Para nosotros, esto es similar a un trayecto de mejoras continuas", comentó Sosa. "Una vez que empezamos, decidimos investigar otras áreas. Y una de las cosas buenas fue la participación del personal de diferentes departamentos. También querían disfrutar de las ventajas y ser parte del grupo innovador".
Ahora el equipo se plantea la actualización a un nuevo MES que se incorporará también a l sistema de IoT y a un nuevo sistema PLM. Fuera de la planta. Bobcat Doosan espera poner en marcha la iniciativa en otros seis sitios de fabricación.
Contenido tomado de: rockwellautomation.com/es