Reconciling the Two Truths of All Industrial Automation Systems
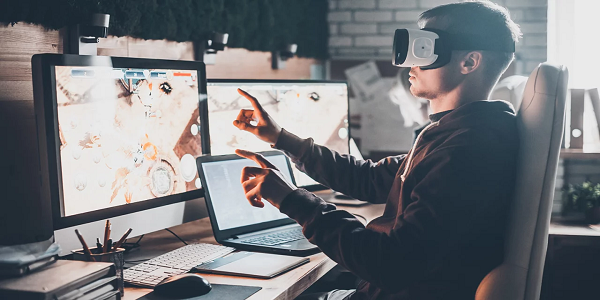
Original content by clicking this link
BLOG | 3 minute read 🕛
I recently met with a client from a large CPG company who said his challenges are rooted in the fact that every industrial automation system comprises two descriptions of the truth, a physical one and a logical one. And because of the development process, these two truths are rarely aligned.
The physical truth is the CAD model of the system or machine, and the logical truth is the control system. Their misalignment comes to a head at the commissioning phase of the project, when they are brought together for the first time. And the result is often a system that operates below expectations in some way, or that requires costly modification to meet the spec.
The two truths don’t need to be misaligned by much for the system to under-perform, but the costs associated with changes and delays at the commissioning stage can have a catastrophic effect on the profitability of the system, and put into question further automation decisions.
A digital twin can bring the two truths together early in the design process, before metal is cut and concrete poured, so the combined operation of the mechanical and the logical systems can be observed, tested, debugged, and verified safely and accurately. As a bonus, there's less conflict between the teams responsible for each truth at this early stage as changes are easier to implement.
Testing Systems in the Digital World
By creating a dynamic digital twin comprising both the CAD and the real operational logic of the system, you have at your disposal a powerful means of putting a system through its paces in a virtual environment, where the cost of changes is minimal compared to those incurred at the commissioning phase.
3D simulation and emulation software provides an ideal platform for creating dynamic digital twins. With it, you can import the CAD from a wide range of standard formats, create kinematic behaviors to reflect the movements of the real system, and connect the model control items to the real control system via a tag browser. Then, you need only create loads to drive the system and your digital twin is live and ready to be operated via the HMIs you’ll use in the real system.
The two potentially conflicting truths are now accurately represented in a virtual environment. Their full operation can be exhaustively and repeatably verified and demonstrated, before committing any resources to their manufacture.
When the real system is assembled on site and connected up to the control system, you can be confident you won’t encounter any logical operation or sequencing issues. They will have been identified and resolved earlier during the virtual commissioning phase of the project.
Winners All Around
A system that has been put through the rigors of virtual testing and commissioning benefits everyone. Production workers gain a more thoroughly tested system that performs to spec. System integrators can predict commissioning times more accurately and plan accordingly. And all stakeholders win when projects come in on time and on budget.
The use of virtual commissioning adds value to the whole process not only by producing tangible returns, but also by raising the level of confidence associated with the process of implementing industrial automation systems.